Turnkey Backhoe Assembly
Case Study:
Global Forestry & Construction OEM
Background
A Forestry and Construction OEM required an efficient and cost-effective solution for their backhoe assembly process. The existing process was labor-intensive, required multiple suppliers, and involved significant logistical complexity. Our expertise in wire forming, welding, and assembly positioned us to deliver a streamlined, turnkey solution that reduced costs and increased production efficiency.
Challenge
The OEM faced several challenges with their tractor assembly:
1. Labor Constraints: Assembly required multiple steps, handling and supplier coordination, leading to inefficiencies.
2. Supplier Complexity: The bill of materials involved seven different suppliers.
3. Assembly Line Disruptions: The process and plant space constraints required a full assembly line refit, leading to costly downtime.
4. Quality & Consistency Requirements: The assembled components had to meet stringent specifications to ensure smooth machine operation.
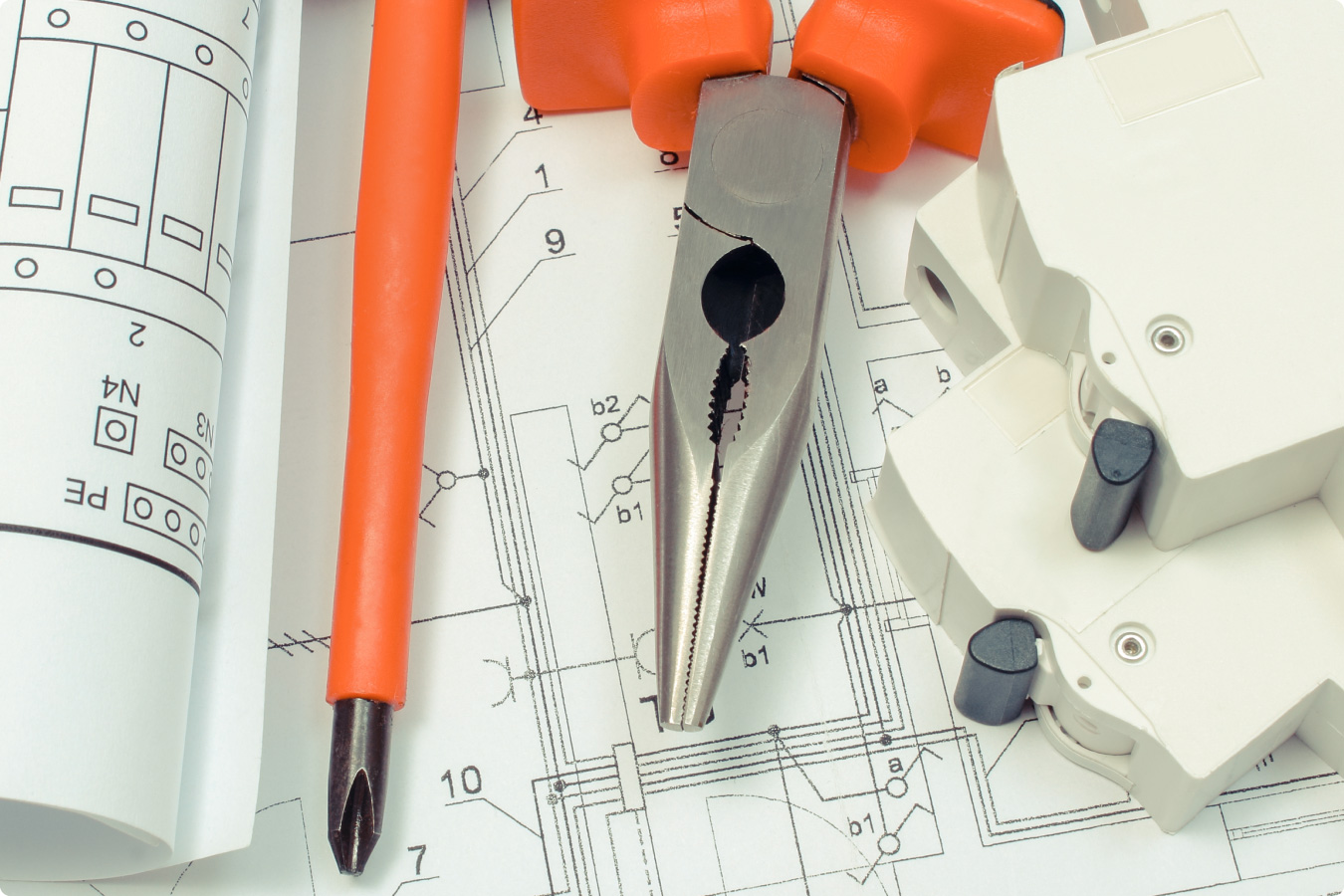
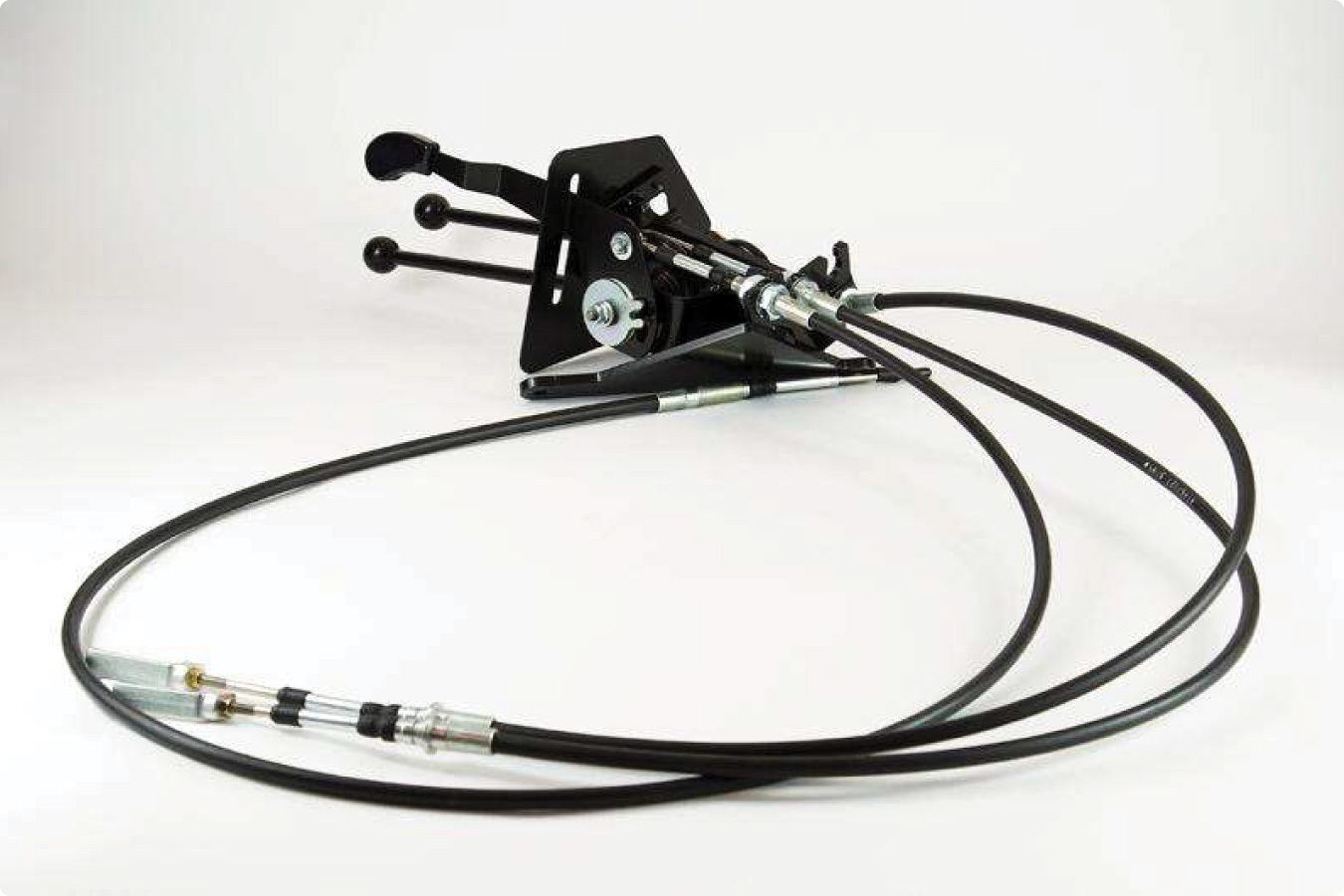
THE WORK
Solution
Our team proposed a fully-integrated, plug-and-play assembly, eliminating redundant handling and simplifying supplier management:
1. Supplier Consolidation: Reduced from seven suppliers to one, simplifying procurement and logistics.
2. Turnkey Assembly: We provided a fully assembled and tested subassembly, ready for direct installation on the OEM’s line.
3. Improved Quality Control: Ensured correct lever movement, torque specifications, and cosmetic integrity.
4. Optimized Logistics: Delivered components with precise labeling and protective packaging to prevent damage and mis assembly.
Implementation Process
1. Opportunity Identification
- Conducted a line walk to assess inefficiencies in the OEM’s current assembly process.
- Proposed integrating multiple components into a single turnkey assembly.
3. Prototyping & Validation
- Created test assemblies to ensure full operational function and compliance with torque and movement tolerances.
- Implemented clear left/right identification for seamless installation.
2. Engineering & Supplier Coordination
- Worked with OEM’s engineering team to refine specifications.
- Sourced additional components from pre-approved suppliers to match existing supply chain requirements.
4. Full-Scale Production & Logistics Optimization
- Established streamlined bolt-on assembly for immediate installation.
- Delivered pre-wrapped, protected, and labeled components per OEM packaging requirements.
- Eliminated the need for additional supplier coordination and assembly labor.
THE BOTTOM LINE
Results & Impact
1. Labor Savings: Eliminated the need for OEM labor to assemble the backhoe subassembly in-house.
2. Supplier Consolidation: Reduced from seven separate part numbers to one, simplifying procurement and logistics.
3. Assembly Line Efficiency: Transitioned form a complex multi-step subassembly process and line refit to a true plug-and-play component.
4. Faster Production Ramp-Up: The streamlined process enabled an immediate implementation, reducing lead times and downtime.
5. Lower Total Cost of Ownership: Reduced administrative, handling, and labor costs while improving quality and consistency.
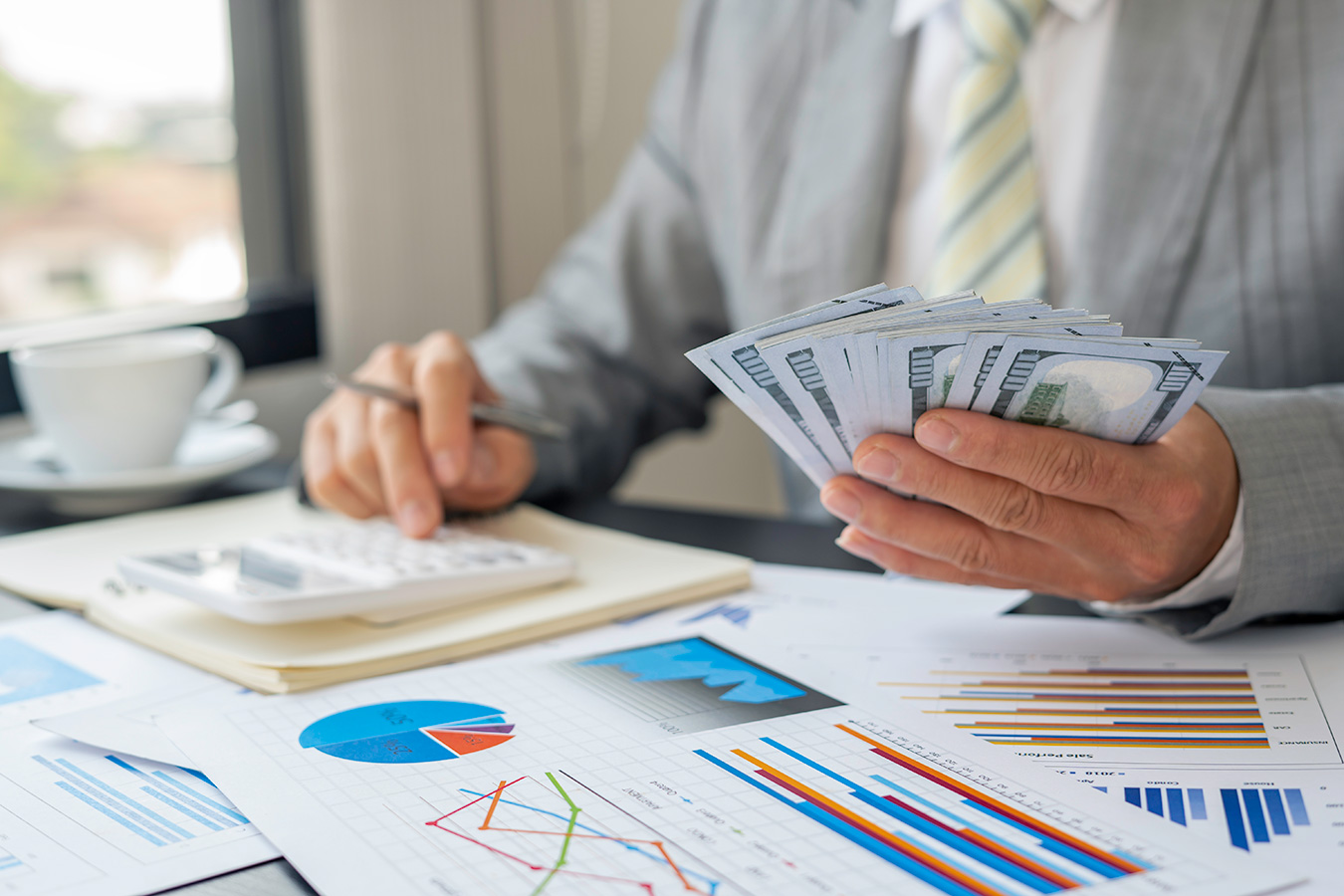
Conclusion
By leveraging our expertise in wire forming, welding, machining, and turnkey assembly solutions, we delivered a fully integrated backhoe subassembly that simplified operations, reduced costs, and improved production line efficiency. Our ability to consolidate suppliers, reduce labor requirements, and ensure plug-and-play installation resulted in a seamless solution for our OEM partner.
Let's Make Something Together!
GET A QUOTEPROUDLY SERVING
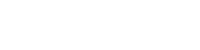
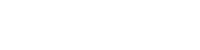
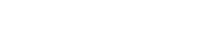
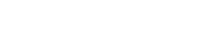
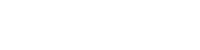
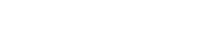